Warehouse Management System 101
Warehouse management systems (WMS) are crucial to the successful operation of a distribution center. They help businesses streamline operations by automating repetitive tasks, managing inventory, and improving logistics. A WMS can also save companies time and money.
It can reduce the amount of human labor needed to complete tasks, which makes it easier for companies to scale their operations. This frees up employees to focus on more important projects that directly impact the bottom line.
If you want to know everything about Warehouse Management Systems, this WMS 101 article is for you to clear all your confusion and doubt. So, let’s dive in!
WMS 101
WMS is a software that helps companies manage their inventory, orders, and distribution. It’s a computer system that automates the movement of goods, materials, and information between locations.
WMS manages the entire process of receiving, storing, picking, packing, and shipping products. This helps improve efficiency in your warehouse so you can take advantage of every square foot for storage or fulfillment.
WMS is often used with a barcode-based inventory management system, also called an automated data collection (ADC) system. This allows you to track the location of your inventory at all times.
What is Warehouse Management System?
A Warehouse Management System (WMS) is a software application that automates the processes of receiving, storing, and shipping products. WMS helps companies to manage their inventory and distribution efficiencies. It is a software solution that can be used by manufacturers and distributors to track and manage their inventory.
A WMS is designed for manufacturing companies. However, but can also be used by distributors. The WMS software can track and manage inventory in a warehouse, monitor and report on shipping. A WMS includes features such as receiving, order processing, packing/labeling, and shipping.
How Does Warehouse Management System Works?
Warehouse Management System (WMS) is software that tracks the location of goods in a warehouse and automates the movement of these goods. It works by creating an integrated system for storing and distributing products efficiently.
The main benefits of WMS are:
- Improved inventory management – This reduces costs by reducing unnecessary storage space, theft, and damage to goods during transport.
- Improved efficiency – This means you can get more done with less effort, as your employees won’t have to manually track inventory levels or perform repetitive tasks such as pricing each product individually.
How WMS Saves Money in Distribution Centers?
Warehouse management systems (WMS) utilize several technologies to improve distribution centers’ processes and capabilities.
By automating warehouse operations, WMS systems have been shown to reduce inventory costs, labor costs, and shipping costs. In general terms:
- Warehouse management systems eliminate the need for manual data entry by enabling computers to track inventory quantities throughout the supply chain. This saves money on labor costs by reducing the amount of time it takes for workers to enter data manually into spreadsheets or databases each day.
- WMS also reduces shipping costs by automating internal processes such as order processing and shipping schedule so that your company can ship products more quickly and efficiently than before having installed a WMS system in place.
A warehouse management system helps businesses to store and distribute products efficiently.
A warehouse management system goes a long way toward making your distribution center more efficient. For example, it can help you to manage and track inventory, coordinate the flow of goods through your facility, improve customer service and reduce costs. Additionally, it increases productivity by providing real-time data that allows you to make informed decisions.
Here are four ways in which WMS helps to improve efficiency:
- Improved inventory management
- Improved supply chain management
- Reduced costs due to automation
- Improved customer service
Speedy Picking and Shipping
Warehouse management systems (WMS) help companies reduce the time required for picking and shipping. This is achieved by automating the process of picking items from a warehouse and moving them to a shipping area. WMS also helps in reducing errors during the process, which otherwise might occur due to human error or lack of knowledge about the location of products.
A WMS allows you to create different pick lists for each user based on their roles and responsibilities, as well as store all information regarding your inventory in one place so that no mistakes are made when it comes time to ship out an order.
The system can also be used to track the number of items picked and shipped, which makes it easier to identify any problems that may arise in the future.
By using a WMS, you can save time and money by reducing the number of errors made during the shipping process. This is particularly helpful for companies that receive large shipments or have a wide variety of products to sell.
Real-time Inventory Management
Real-time inventory management is another important feature of a WMS. It helps to maintain good customer service by preventing out-of-stock products and stock overages.
Customers hate it when they cannot find what they are looking for in a store or can’t get the product they want because it has sold out. This can happen due to a poor inventory system, which leads to unhappy customers and lost sales.
A well-designed WMS will provide you with accurate data on how many items are in stock at any given time, allowing you to easily keep track of how much product is available for sale at any given time.
Speedy Picking and Shipping
If you don’t have a warehouse management system, your picking and shipping process can be slow and painful. When multiple people are involved in the same task, there is always concern about the accuracy of their work. With WMS, everything happens automatically; thus, there is no room for human error to creep in.
WMS also helps reduce errors in picking by providing real-time data on stock levels (and other indicators) so that service providers can make more informed decisions when they are selecting which items need to be shipped first.
This means that you don’t have to worry about running out of stock and missing an important order, which is a common problem with manual processes.
Improved Customers Experience
Your customers are the reason why your business exists. They’re the reason you make money and grow. If a customer has a bad experience with you, they will not come back to you again.
This is especially true in the world of eCommerce, where there are so many options for customers to choose from when buying products or services online.
If you run an eCommerce store, your customers must have a great experience with your company every time they buy from you!
Reduce Labor Costs
One of the biggest benefits of a WMS is that it automates manual processes. This means that you can reduce the amount of labor required to run your business. Automating manual processes will also allow you to serve more customers while reducing costs.
For example, if you have a warehouse that uses manual labor for picking products, then it might take 10 hours for two people to pick and pack 100 units of product. But with a WMS, this process could be done in just 30 minutes!
It might seem like a lot of work to install and configure a WMS for your business, but it’s really worth it. The benefits of using a WMS will help you save time and money while providing customers with a better experience!
Enhanced Order Accuracy
To start, WMS helps you get the right product to the right customer at the right time. When orders are entered into a warehouse management system, they can be automatically distributed to multiple picking locations and routed back to shipping.
This means that if an order is placed by phone or online, it will be updated in your system automatically. If a customer has ordered several different products and they arrive at various times throughout the day, they will be assigned to different trucks so there’s no chance of them being delivered together or on top of each other (which could result in damaged goods).
The WMS also allows you to see where all of your inventory is located and who has access to it. This means that if an employee makes a mistake when placing an order—or even worse—someone else’s order gets shipped instead (because he/she looked like them), it can easily be tracked down and corrected with minimal disruption.
Increased Productivity
A Warehouse Management System (WMS) helps to increase productivity in your warehouse by reducing the amount of time spent on manual tasks. It is also important to note that WMS can help you get more done in less time, which means that your employees will be able to complete their shifts faster than ever before.
Another way that WMS can improve productivity is by improving the efficiency of your warehouse workers. This results in fewer mistakes, less downtime, and higher profit margins for businesses that use this kind of technology.
Reduced Inventory Losses
Inventory loss is a major problem in the warehousing industry. According to the Association of Operative Millers (AOM), there is an average annual inventory loss of 1.5% for grain storage facilities in the United States, with losses as high as 10% reported by some companies. This means that every year, US businesses are losing millions of dollars in revenue every year due to faulty equipment and poor management practices.
Inventory systems have always been used to help reduce inventory loss. Still, with today’s technologies, it’s easier than ever before to use data analytics tools to optimize your warehouse operations and boost profits through:
- Real-time information about the location of goods (for example, via RFID).
- Automatically reordering when stock levels are low (for example, via WMS)
Why is Warehouse Management System Important?
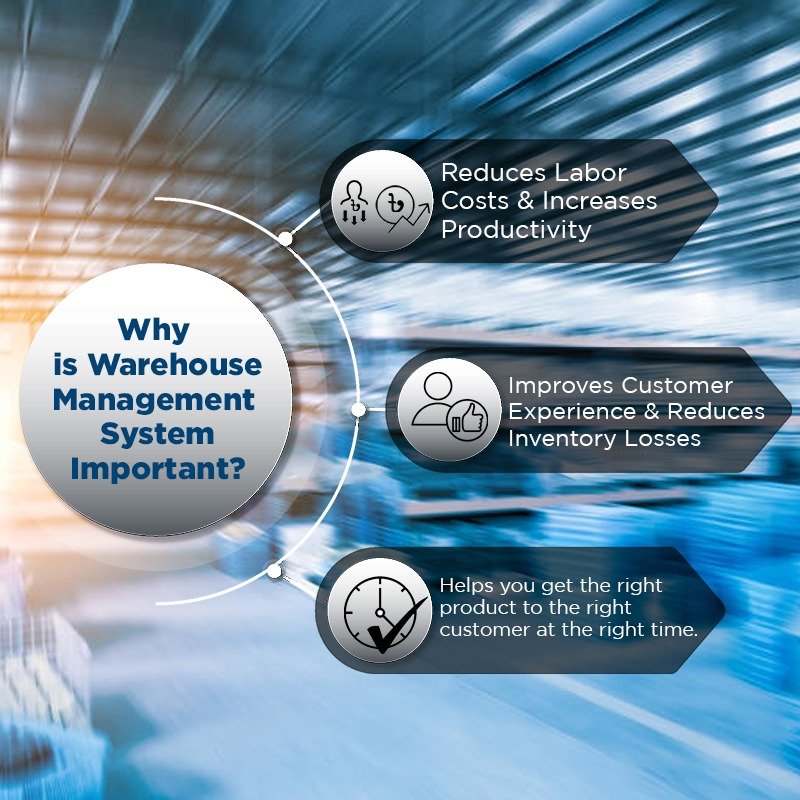
Reduces Labor Costs & Increases Productivity
The WMS improves productivity by automating most of the tasks and reducing the need for manual labor. It also reduces labor costs as fewer workers are required to perform the same task, thus reducing payroll expenses. Warehouses with a high volume of inventory require large numbers of employees who need to be paid on time every month. By using WMS software, these costs can be significantly reduced or eliminated altogether, leading to significant savings on your part without affecting your service levels or product quality at all!
Improves Customer Experience & Reduces Inventory Losses
With its ability to track every single item that enters/exits your facility at any given moment (even if they’re just passing through), you’ll always know exactly what’s where at all times – which means no more lost items! This feature alone lets customers feel confident about ordering from you again, knowing that nothing will ever go missing during transit anymore!
Advanced Warehouse Management System
Advanced Warehouse Management System (AWMS) is a software that helps to manage the entire warehouse operations. It is an integrated system that manages all the warehouse processes such as receiving, storing, picking, and packing of goods at an automated level with advanced features like barcode scanning and RFID tagging.
AWMS can help in reducing labor costs by automating manual tasks and making them easier to manage without any errors. If you want to use WMS for your logistics company or distribution center, then you need to understand each of its components – from planning inventory levels based on sales data using computer software programs to tracking deliveries via GPS devices mounted onto trucks so that drivers don’t get lost along their route.
Conclusion
As you can see, warehouse management systems are a must-have for any business. They offer an efficient way to store and distribute products, which means less time spent on unloading trucks, restocking shelves, and labeling boxes. The technology has also improved customer experience by providing accurate order tracking information and quick response times from support agents.